Pressure vessels
We design and manufacture custom-made solutions, adapting to the specific needs of each project.
Desing and Manofacture of Hing-Specification pressure vesseles
At VR Ingeniería, we design and manufacture specialized pressure vessels for installations in refineries, pumping stations, and compression stations, tailored to a wide range of critical industrial applications, such as:
- General Service
- Lethal Service
- Wet H2S Service
- Hydrogen service
- Amines service
Our vessels are designed to withstand high pressures, ensuring an optimal level of safety and reliability in every project, even under the most demanding conditions.
We design custom equipment
We design custom pressure vessels to meet the specific needs of each client. Our team of experts utilizes specialized software to perform mechanical calculations and structural integrity assessments. This ensures optimal performance, maximum safety, and durability in each of our vessels.
We comply with the most stringent industry regulations, and our processes align with international standards of quality and safety. This commitment ensures our clients’ trust and contributes to building a safer and more sustainable future.
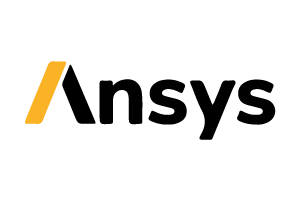
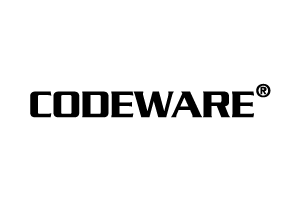

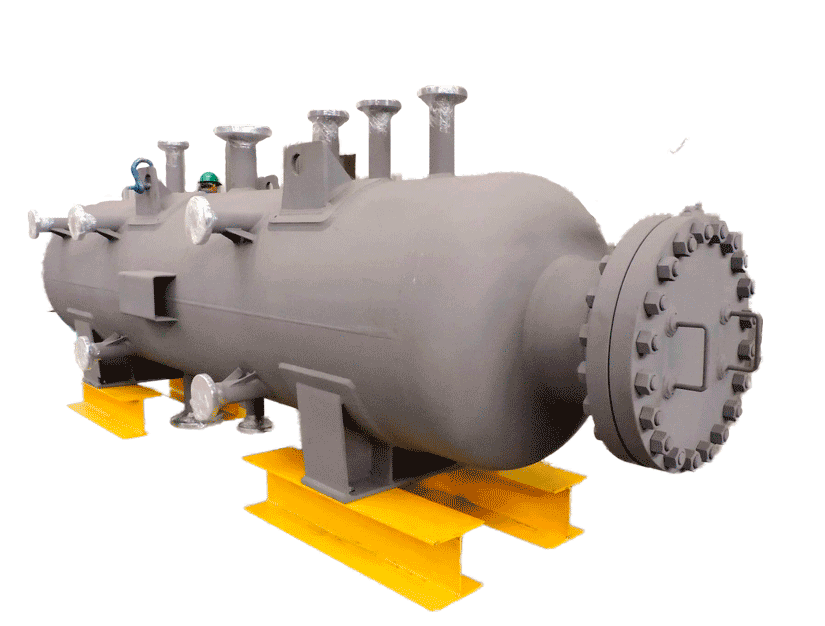
Energy Efficiency:
We design our equipment to maximize heat transfer, which can result in more efficient energy use. This can reduce operating costs and greenhouse gas emissions.
Customization
We have the capability to design and manufacture custom heat exchangers to meet the specific needs of each customer. This can result in products that are better adapted to the plant's operations and can improve its performance.
Versatility
We design for a wide range of temperatures and pressures, making them suitable for various applications.
Quality
All our heat exchangers are subjected to rigorous testing and quality assurance tests to guarantee their performance and durability. Our commitment to quality is unwavering.
Durability
Thanks to precise material selection and a detailed manufacturing process, our heat exchangers are more durable and require less maintenance. This can reduce long-term costs and minimize plant downtime.
Regulatory Compliance
All our products comply with industry regulations and standards, such as the ASME code. This ensures the safety and efficiency of the heat exchangers.
Technological Innovation
We invest in research, innovation, and development to provide heat exchangers that utilize the latest technologies and materials available, aiming for improved performance and greater energy efficiency.
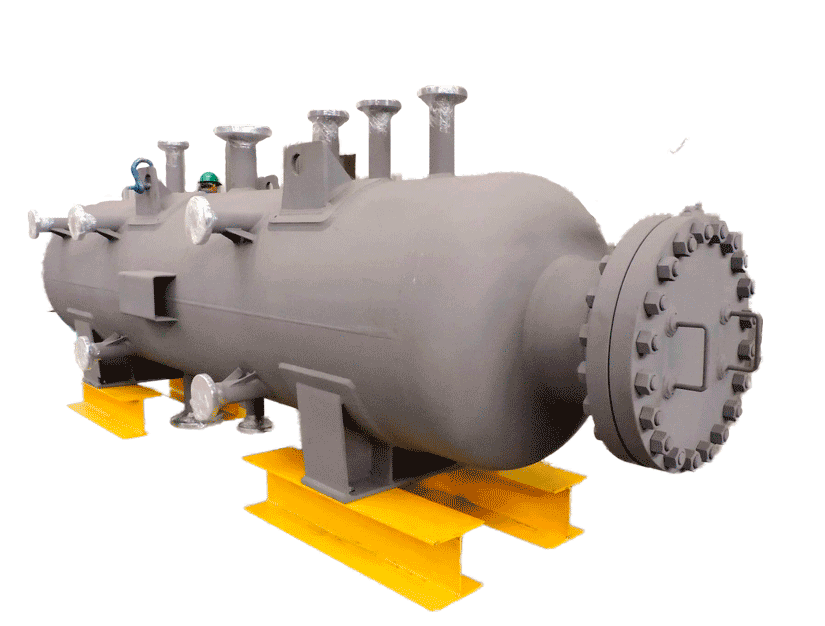
We design our equipment to maximize heat transfer, which can result in more efficient energy use. This can reduce operating costs and greenhouse gas emissions.
We have the capability to design and manufacture custom heat exchangers to meet the specific needs of each customer. This can result in products that are better adapted to the plant’s operations and can improve its performance.
We design for a wide range of temperatures and pressures, making them suitable for various applications.
All our heat exchangers are subjected to rigorous testing and quality assurance tests to guarantee their performance and durability. Our commitment to quality is unwavering.
Thanks to precise material selection and a detailed manufacturing process, our heat exchangers are more durable and require less maintenance. This can reduce long-term costs and minimize plant downtime.
All our products comply with industry regulations and standards, such as the ASME code. This ensures the safety and efficiency of the heat exchangers.
We invest in research, innovation, and development to provide heat exchangers that utilize the latest technologies and materials available, aiming for improved performance and greater energy efficiency.
Features
MATERIALS |
---|
|
Types of vessels |
---|
|
Coatings |
---|
|
Manufacturing Processes
We are a company specialized in the manufacturing of pressure vessels, developed under strict quality standards and processes that ensure reliable performance in high-demand conditions.
Each phase of production, from design to delivery, is managed with precision to ensure operational safety, mechanical strength, and a long service life of the equipment.
We use high-quality welding techniques to ensure the integrity of our pressure vessels. Our trained and certified welders guarantee joints that withstand the high pressures and temperatures typical of the most demanding operational conditions, ensuring reliability and safety in every piece of equipment.
Our precision machining processes allow us to manufacture components with exact tolerances, ensuring a perfect fit and optimal performance of our pressure vessels.
We use rolling forming techniques to shape the components of our pressure vessels, ensuring the dimensional accuracy and mechanical strength required to operate in demanding conditions.
All our equipment undergoes rigorous testing to ensure performance and durability. This includes pressure tests to verify the strength of materials and welds and leak tests to confirm the efficiency of the joints.
Solutions by Industry
Pressure vessels play a key role in multiple industries due to their ability to safely and efficiently contain and transport fluids under high-pressure conditions. At VR Ingeniería, we design and manufacture custom solutions tailored to the operating conditions and specific requirements of each project.
Certifications and Regulatory Compliance
We manufacture according to the specifications of leading global process licensing companies, including Axens, UOP, Kellogg, and Exxon, among others. Additionally, we comply with the highest international standards:
-
ASME Sección VIII, División 1 & 2:
U and U2 certification for the design and manufacture of pressure vessels." -
API 934-C:
Standard for the manufacture of thick-walled chromium-molybdenum steel vessels used in high-pressure hydrogen services. -
NBBI (National Board of Boiler and Pressure Vessel Inspectors):
Inspection and Repair of Pressure Vessels. -
NACE MR-0103, MR-0175, SP-0472, 8X194 :
Standards for Corrosion Resistance in Hydrogen Sulfide Environments. -
ISO 9001:2015, ISO 14001:2015, ISO 45001:2018:
Quality, Environmental, and Occupational Health and Safety Management Systems.
Transforming Challenges into Opportunities
Success Stories
Explore one of our most prominent projects and learn in detail how our solutions have created significant and positive impacts for our clients.
REACTOR
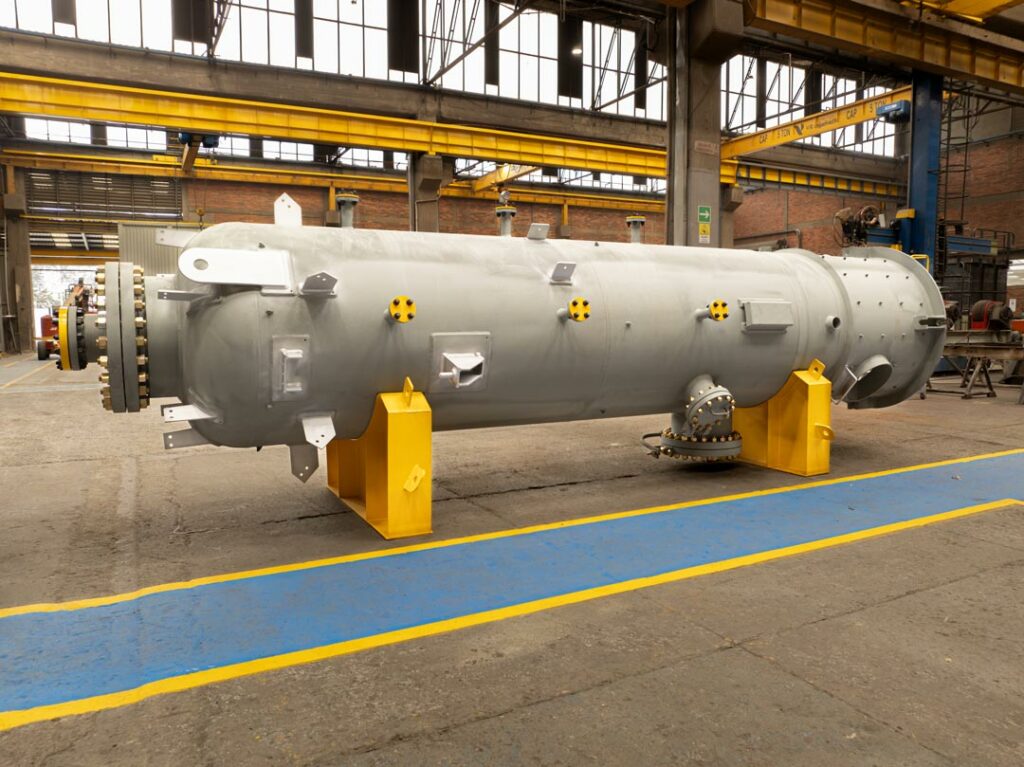
Applications
Refineries, lethal services, and general services.
Pressure range: From 15 psig to 5,000 psig.
Manufacturing processes: Rigorous selection and inspection of materials
Application of specialized welding techniques
Destructive and non-destructive testing to ensure structural integrity.
Compliance with API 934C standard for the fabrication of thick-walled chrome-moly steel vessels used in high-pressure hydrogen services.
Dimensions: Diameter: 55” (1397 mm).
Length: 170” (4318 mm)
Thickness: 1” (25.4 mm)
Materials: Shell: SA-387 GR 11 CL2
Connections: SA-182 F11 CL2
DIESEL SIDE STRIPPER
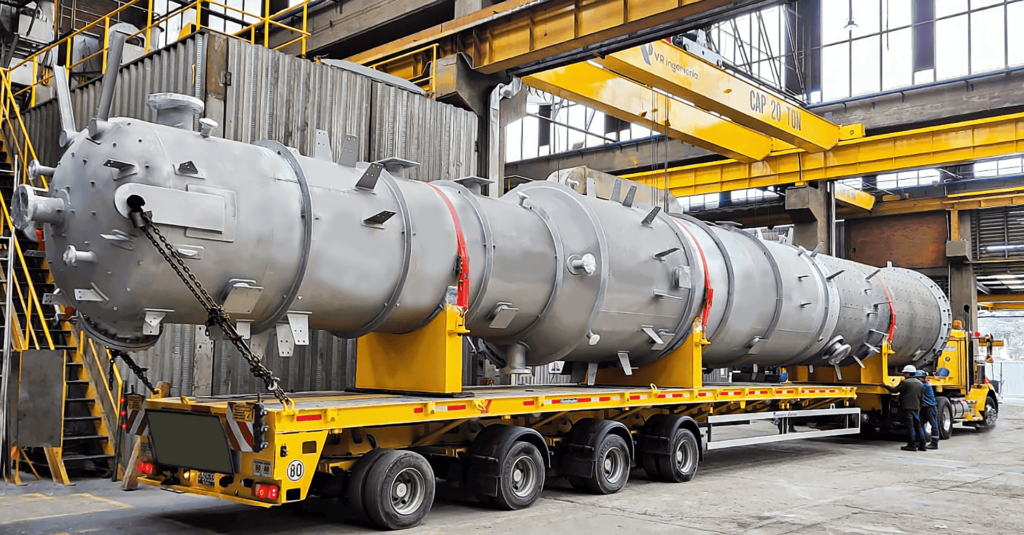
Applications
Refineries, lethal services, and general services.
Manufacturing processes: ASME Section VIII Division 1.
Design Temperature: 650 °F.
Destructive and non-destructive testing to ensure structural integrity.
External Design Pressure: Half Vacuum. Dimensions: Internal diameter: 72” (1900 mm) and 96” (2438 mm). Length: 810” (20,574 mm).
CRUDE OIL, WATER, AND GAS SEPARATORS
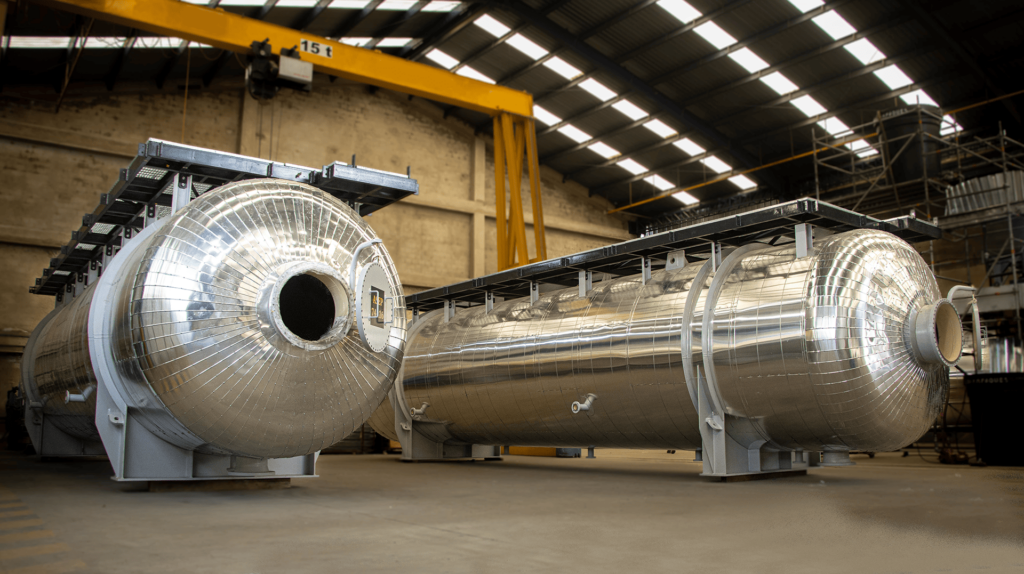
Applications
Refineries, lethal services, and general services.
Pressure range: 100 psig.
Manufacturing processes: ASME Section VIII Division 1.
Destructive and non-destructive testing to ensure structural integrity.
Design internal temperature: 250 °F. Dimensions: Length: 118” (2997 mm).
Our Valuable Client Portfolio
Here is a brief list of clients who have trusted our expertise and quality in the development of pressure vessels.
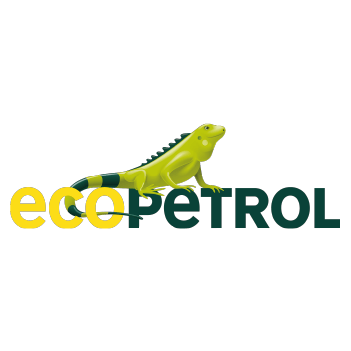
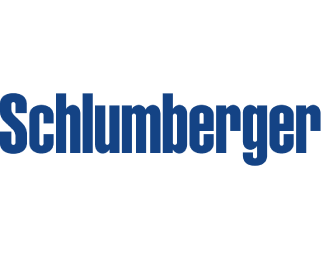
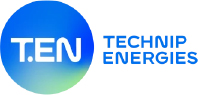
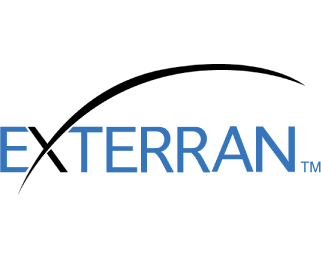
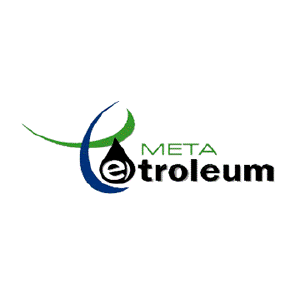
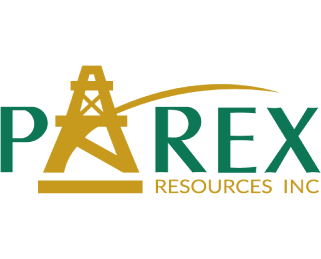
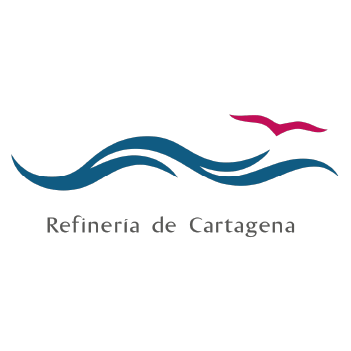
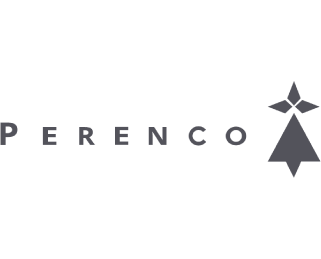
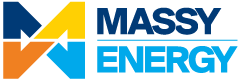
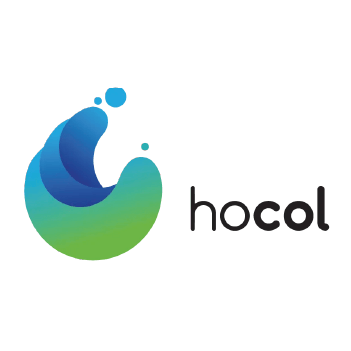
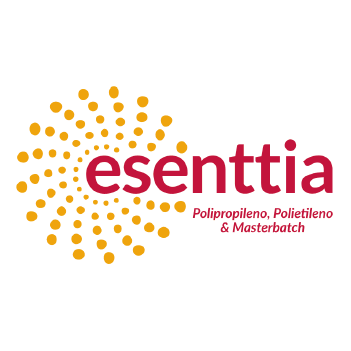
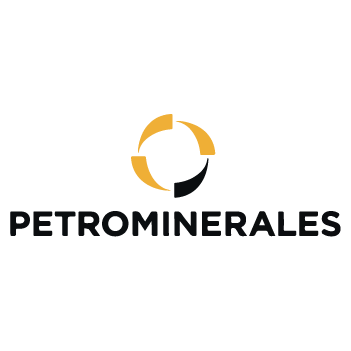
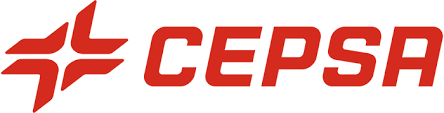
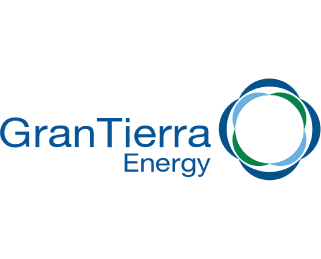
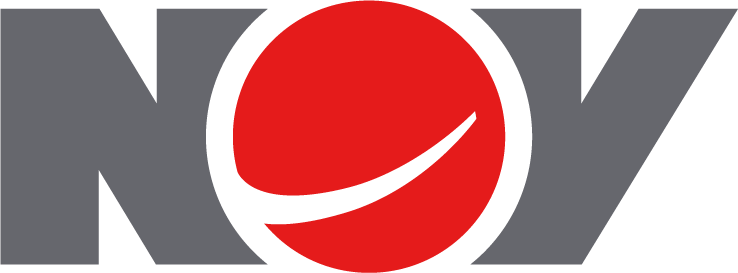
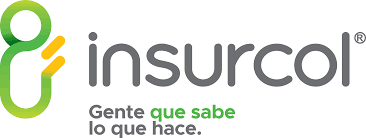
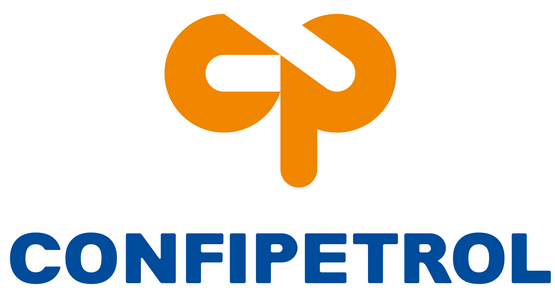
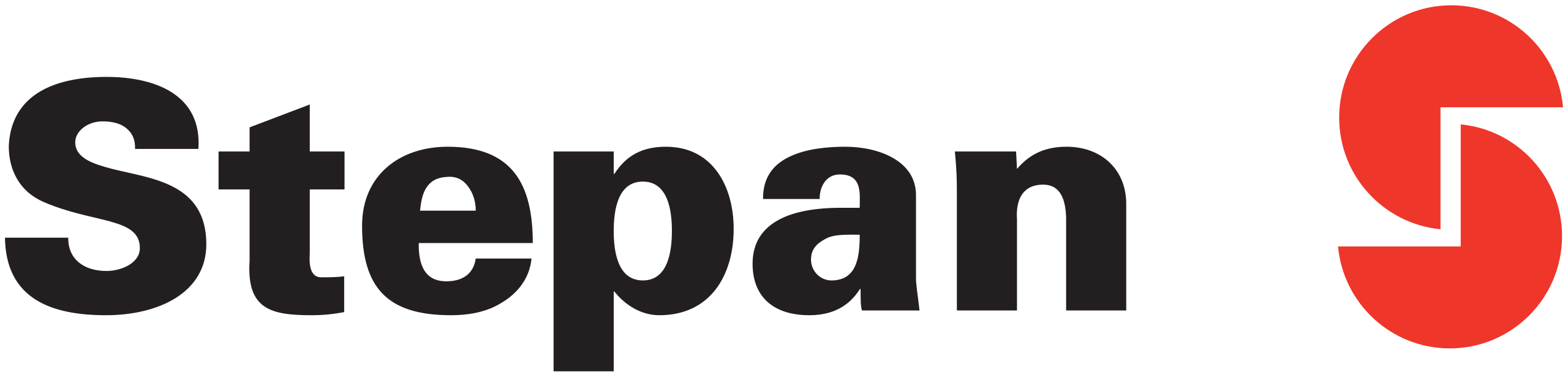
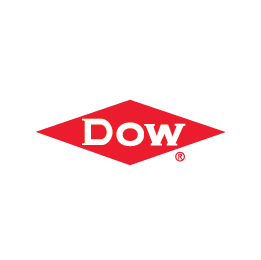
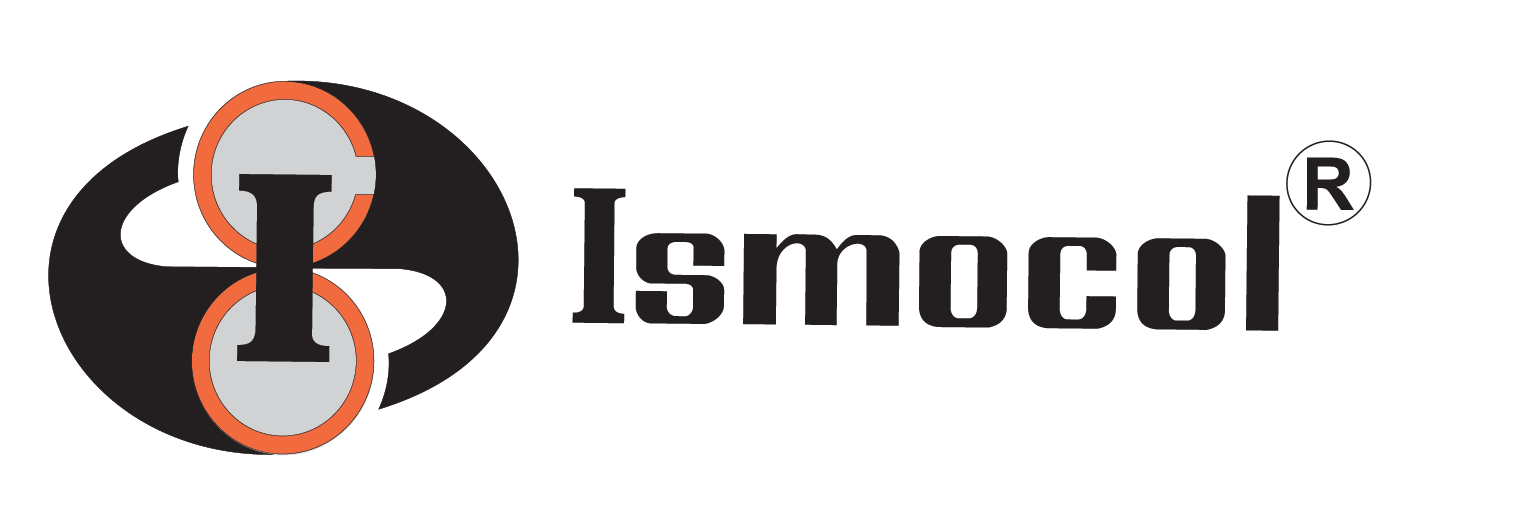
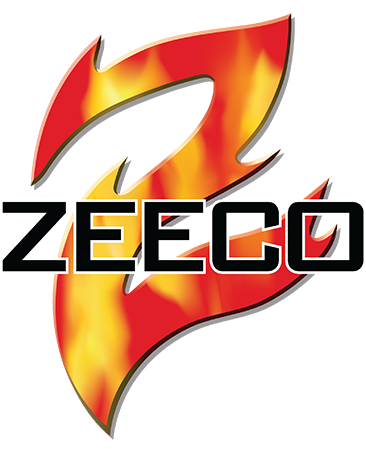
Contact us
Do you have any questions or need more information?
¡Contact us! We are ready to help you.