Steam generation systems
Integrated and Specialized Solutions for the Steam Production Industry.
Optimization for Process Efficiency.
In today’s dynamic industrial landscape, the ability to make sound and timely decisions is crucial for maintaining a competitive edge. Simply incorporating the best equipment into our production systems is no longer enough. It is essential to integrate and interconnect these devices so that they operate in a coordinated manner, functioning as an integrated system. This approach not only optimizes efficiency but also enhances overall performance.
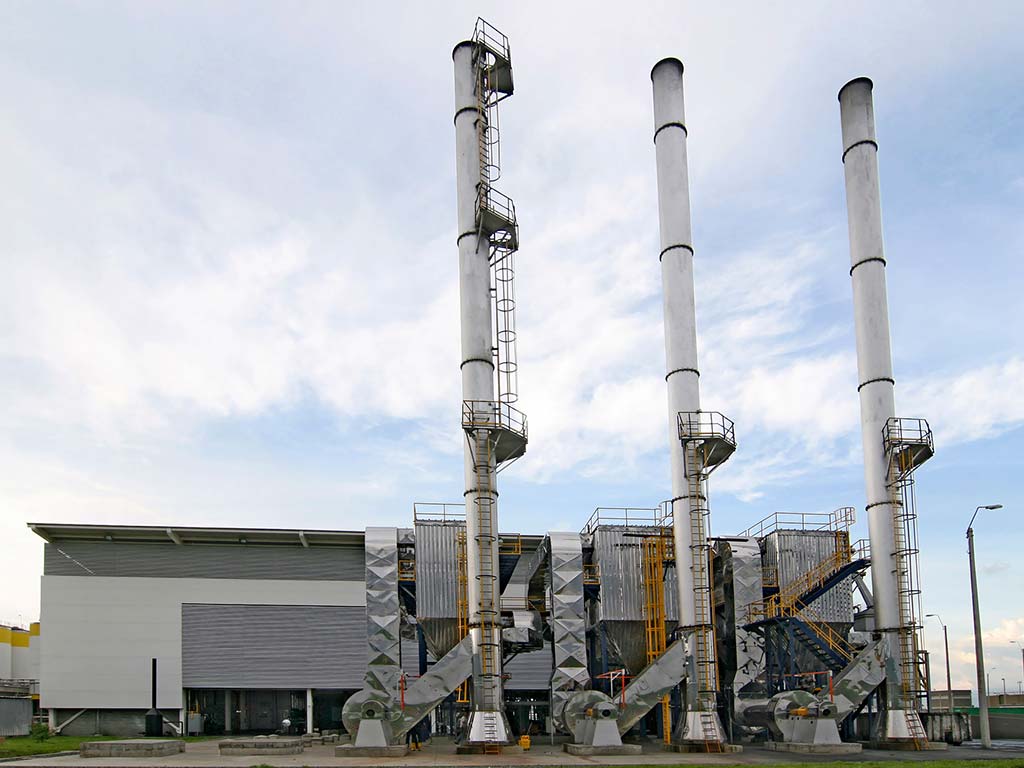
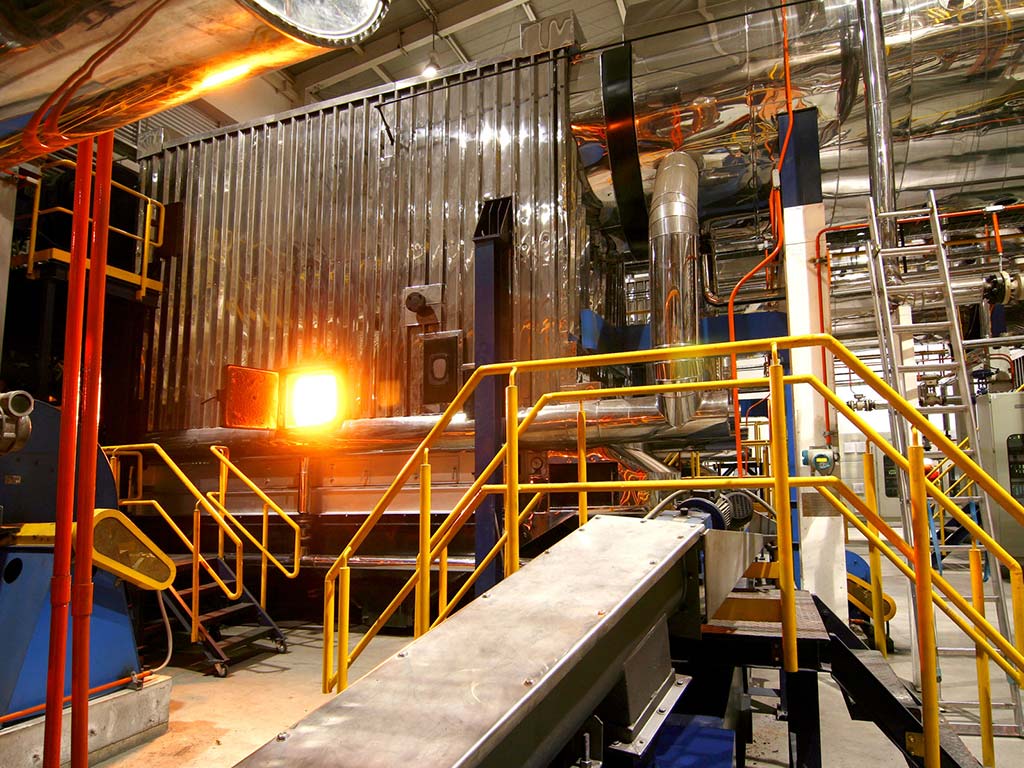
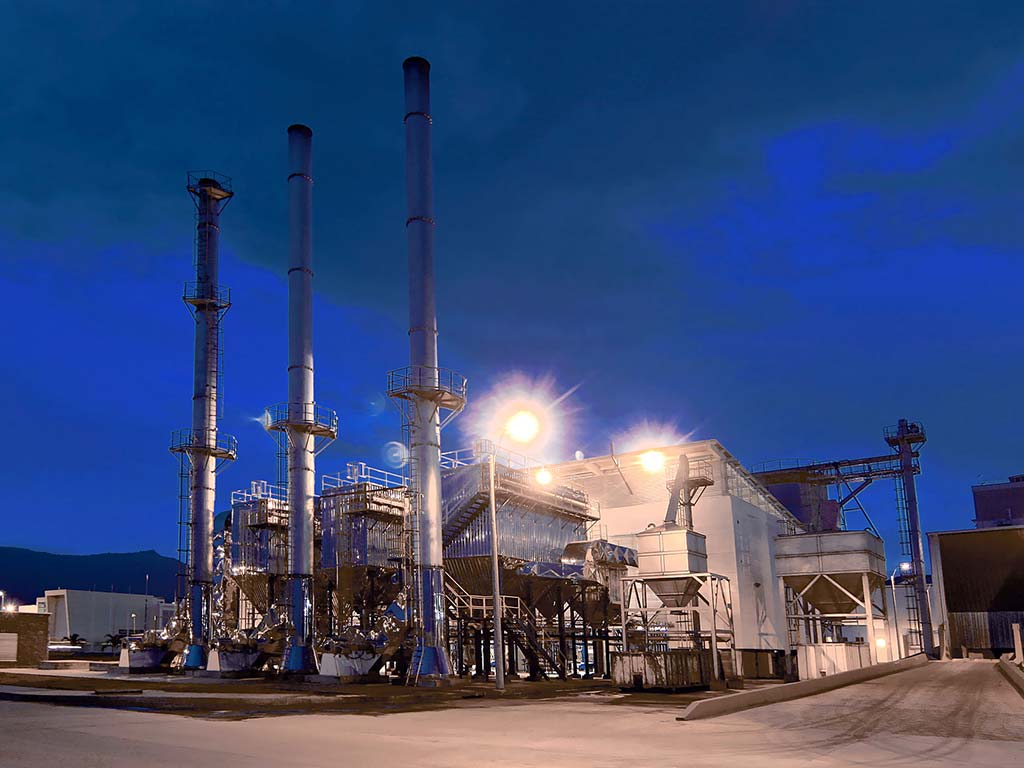
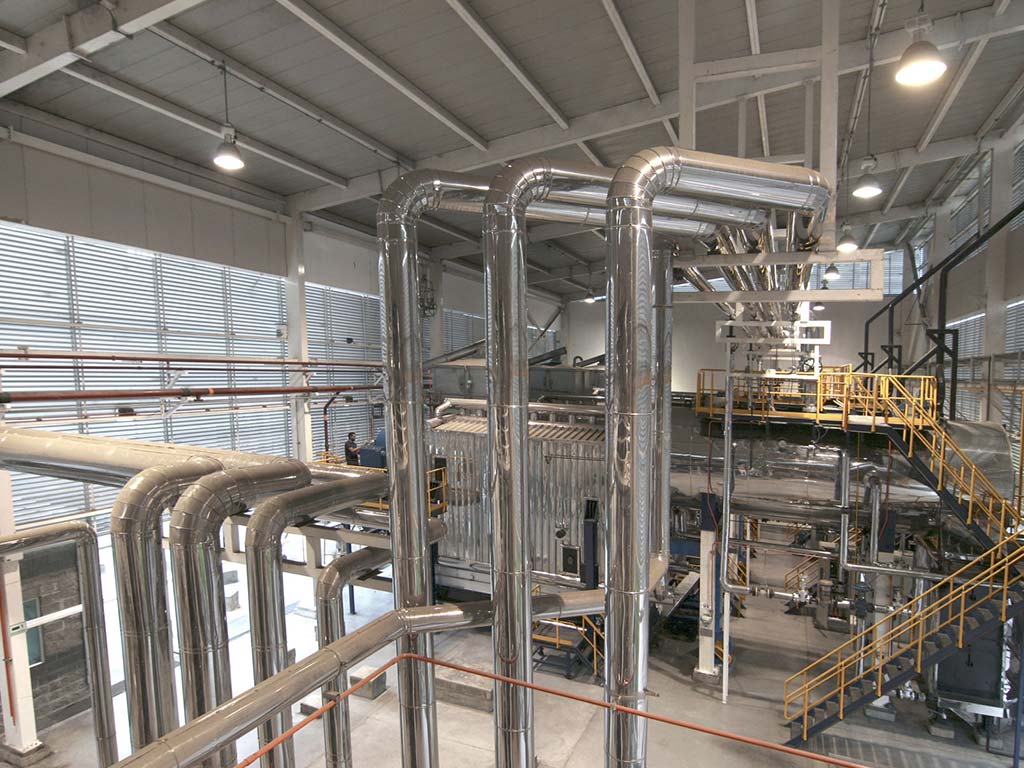
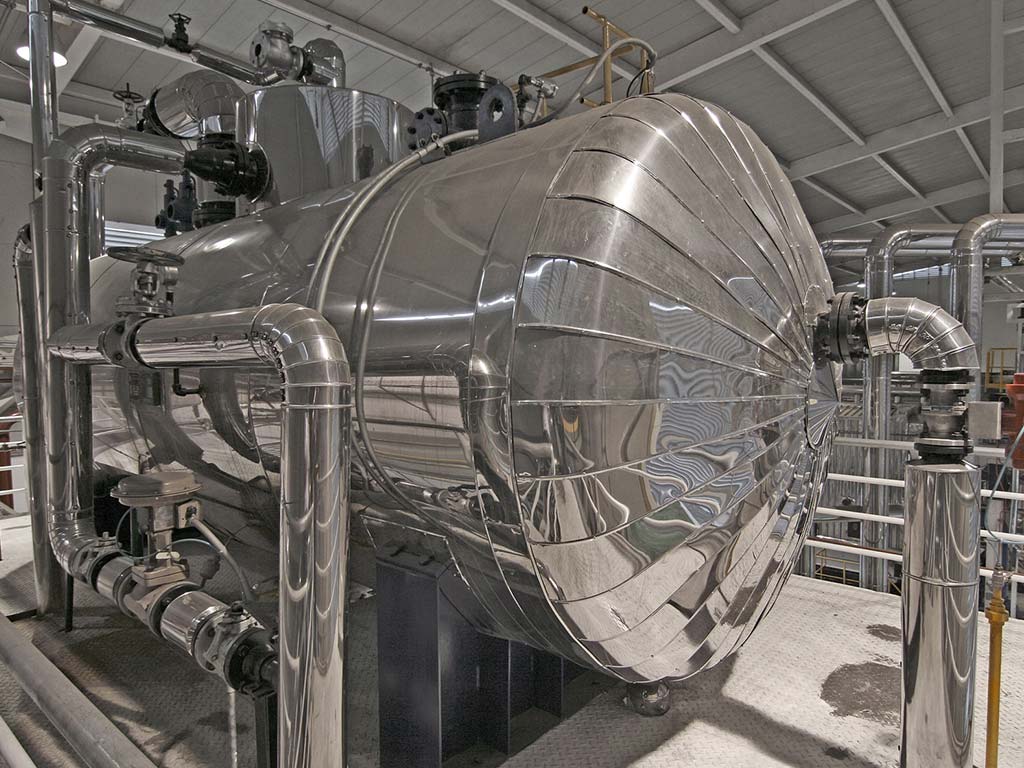
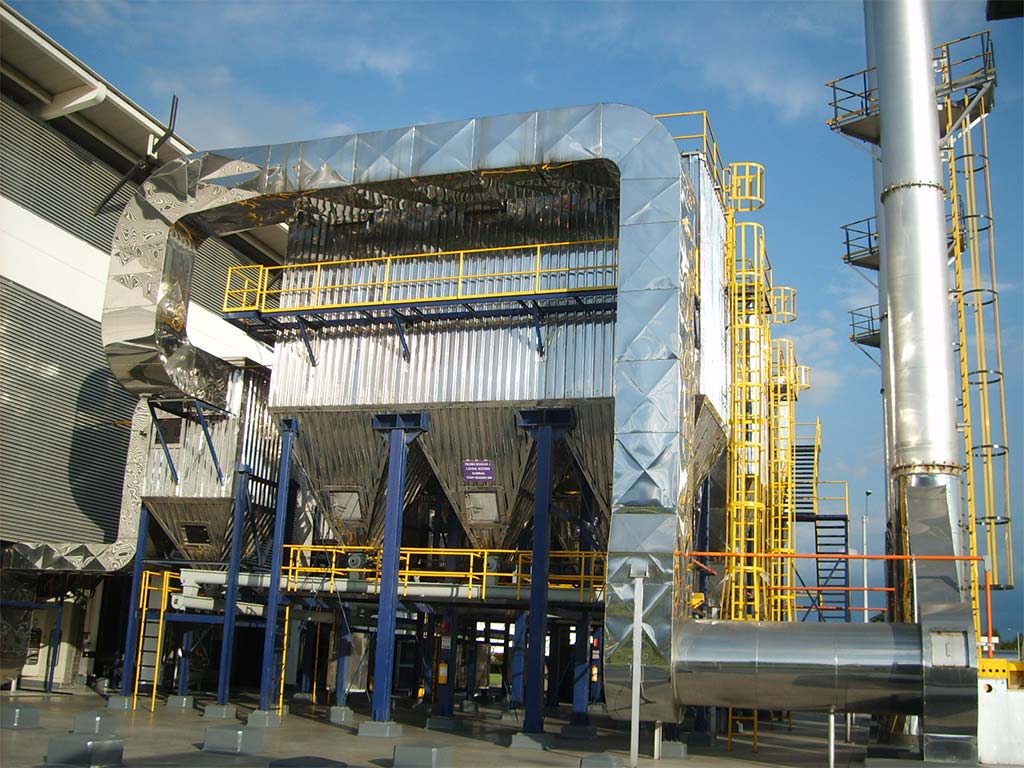
Steam Generation Plants
Our ability to integrate and connect various disciplines allows us to offer customized turnkey solutions tailored to the specific needs of each client. We focus on optimizing production results in key areas such as supervision, combustion control, environmental control, maintenance and energy efficiency. Furthermore, we ensure regulatory compliance through continuous support, guaranteeing that our manufacturing quality is not only maintained but elevated to even higher standards.
These solutions are designed to make the operation of boilers intended for steam production more practical and efficient in the petrochemical, food, and electric power generation sectors.
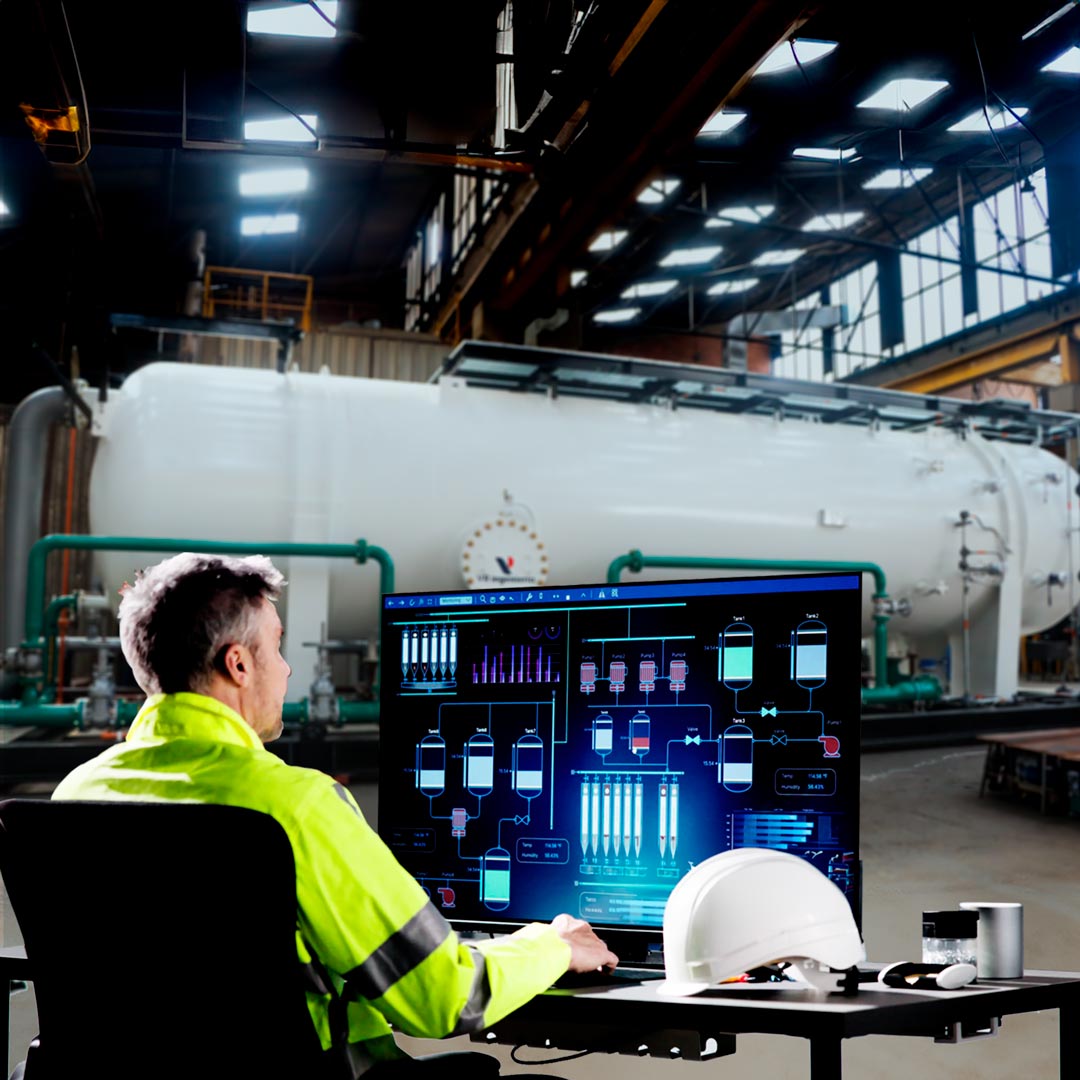
Supervision
The integration of HMI, SCADA, MES, and ERP systems provides an advanced solution for control, supervision, analytics, and data management. It integrates precise instrumentation to monitor and manage industrial processes efficiently, enabling centralized and real-time control while facilitating continuous supervision of multiple operational variables.
- SCADA Control System
- Instrumentation
- Control
- Indicator Report
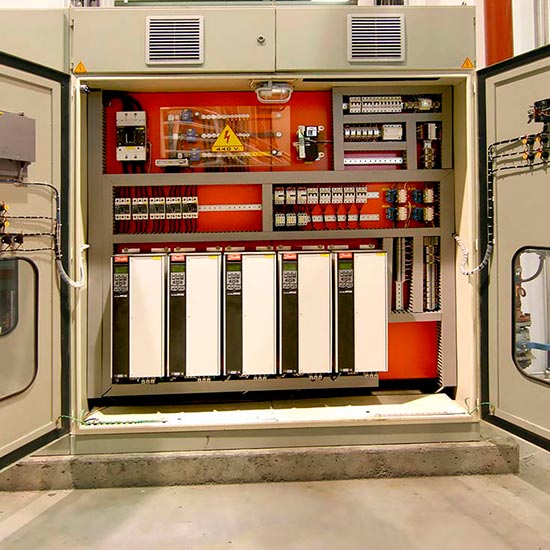
Combustion Control
Combustion control with intelligent dosing and modulated burners represents a crucial innovation in industrial energy efficiency. By precisely adjusting the air percentage in combustion processes, a significant reduction in unburned residues is achieved, optimizing performance and minimizing environmental impact.
- Intelligent Dosing
- Control % O2
- Modulated Burners
- Reduction of Unburned Residues
- Reduction of Fuel Consumption
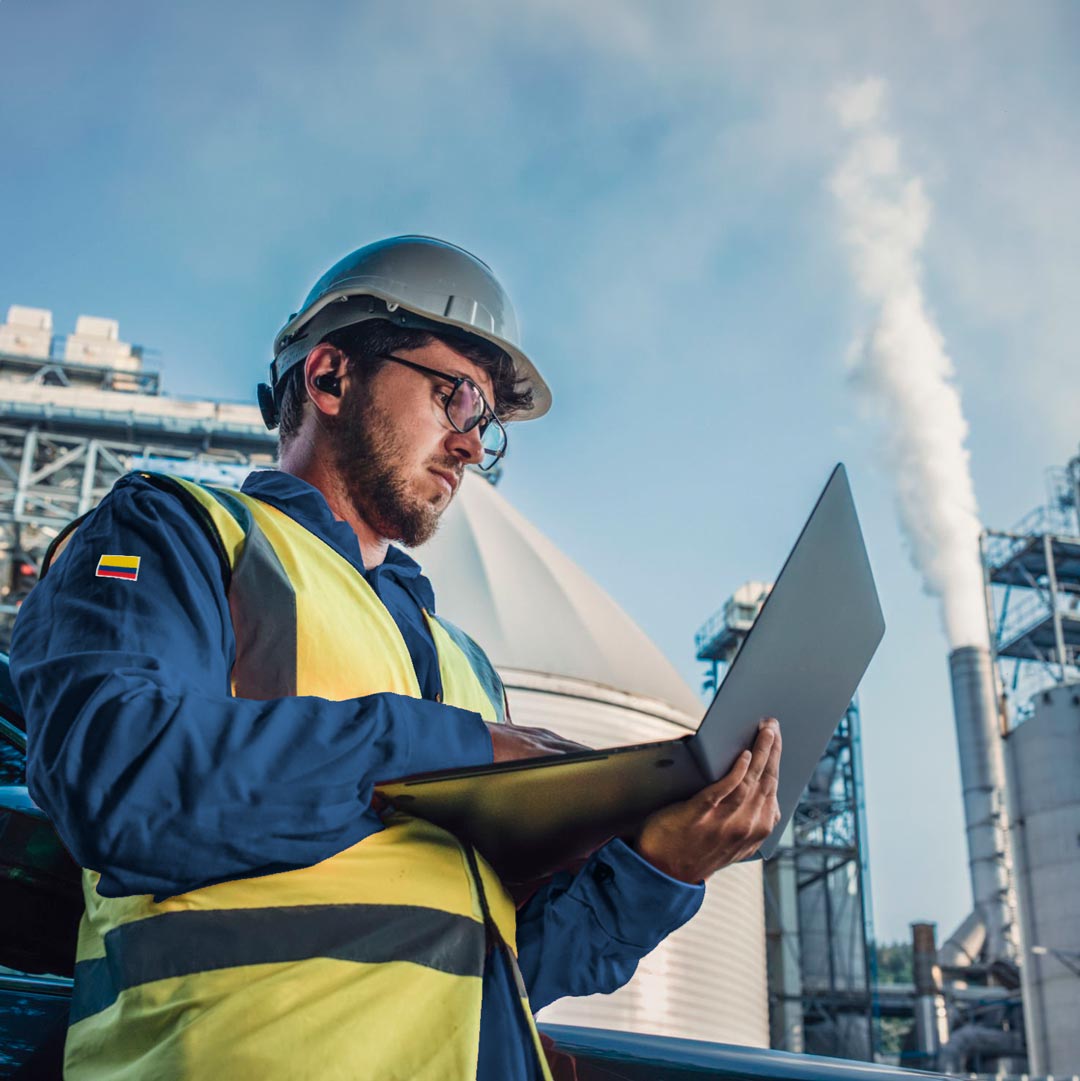
Environmental Control
These advanced systems enable the efficient capture of particulate matter and pollutant gases, ensuring compliance with stringent environmental regulations.
- Bag Filters
- Desulfurizers
- Electrostatic Precipitator
- Emissions Reduction
- Cyclones
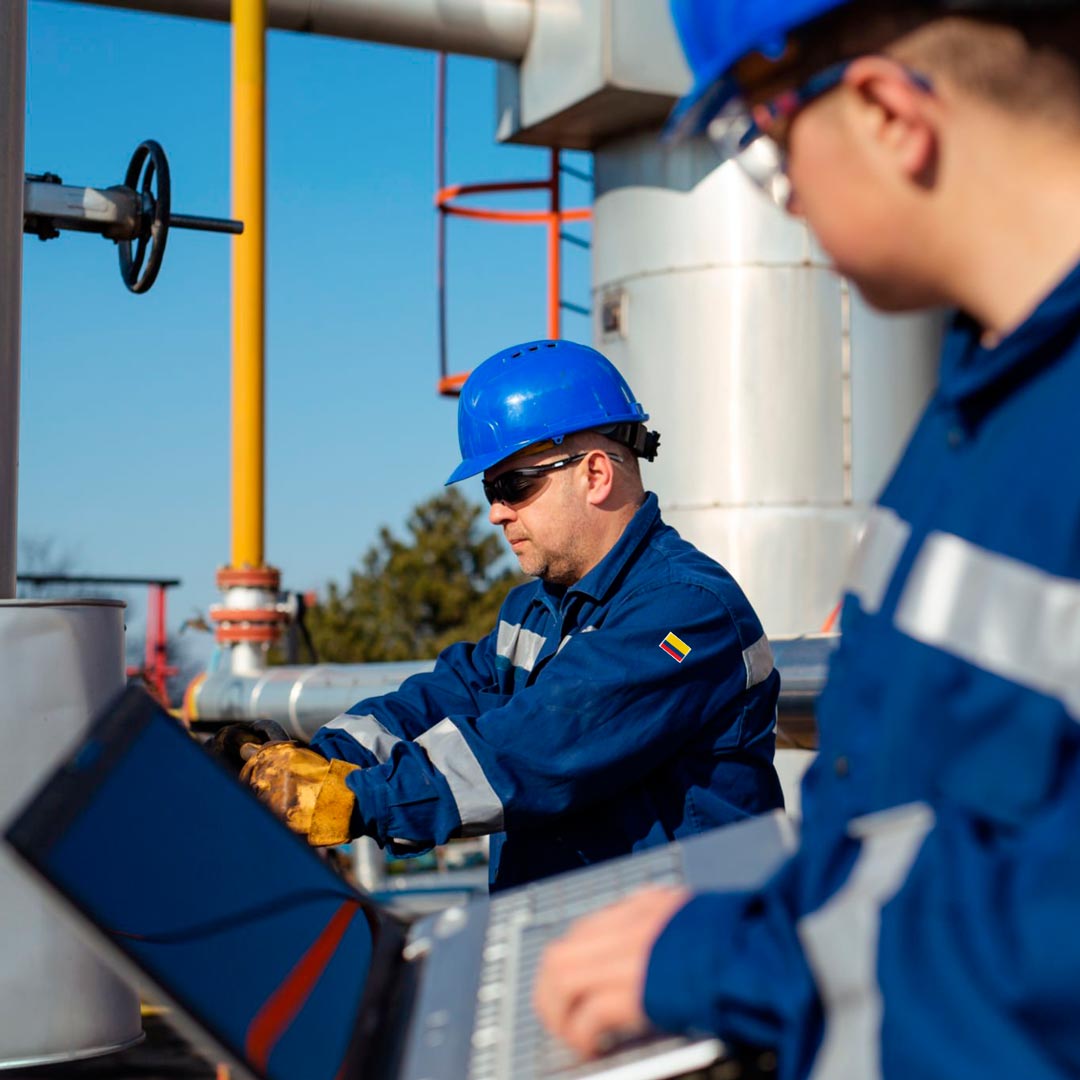
Maintenance
These practices ensure that industrial systems operate optimally and safely, minimizing downtime and maximizing asset lifespan.
- Diagnosis
- Standardization of Routines
- Calibration
- Upgrade
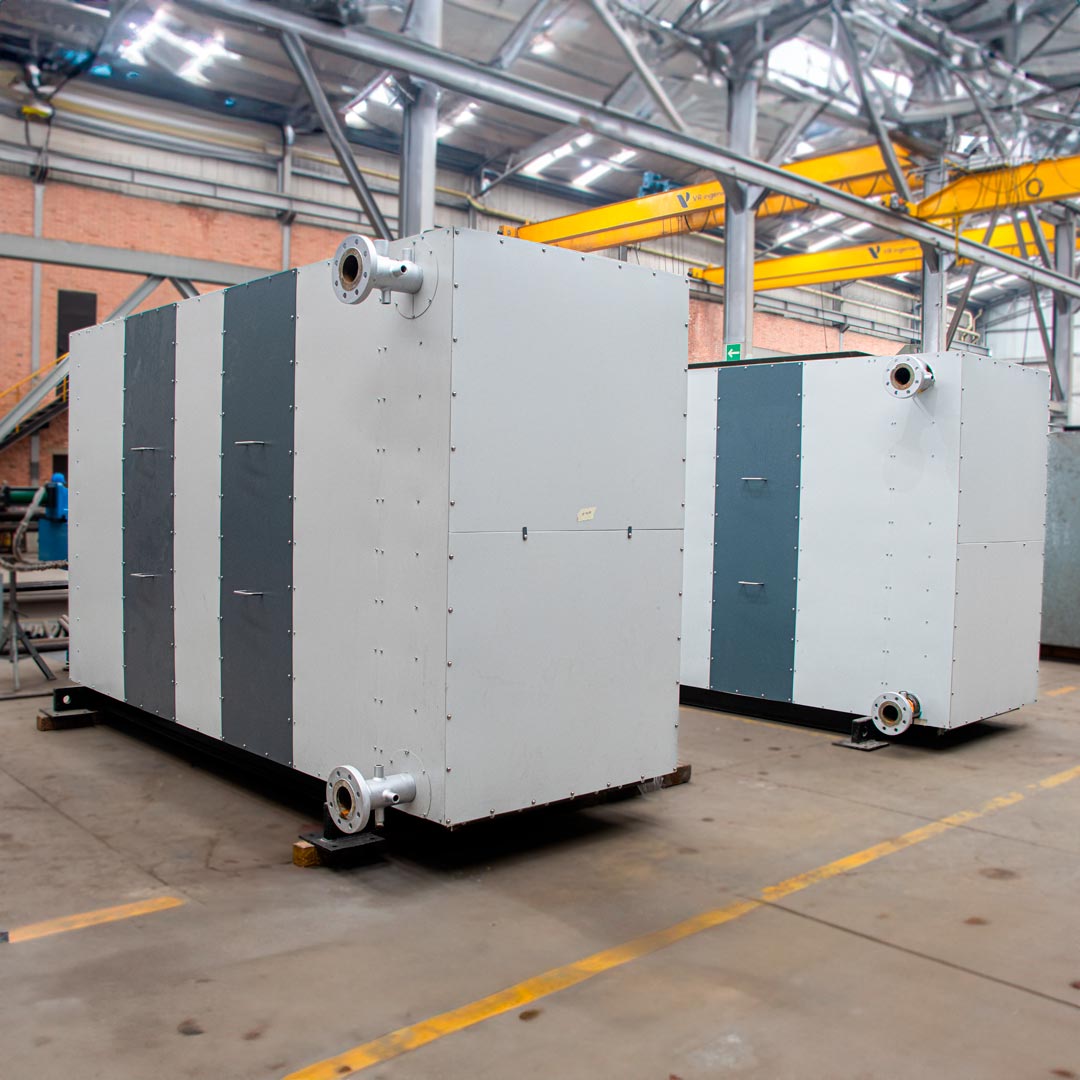
Energy Efficiency
The use of specialized equipment to optimize energy consumption represents a substantial reduction in operating costs and improves environmental sustainability.
Adaptation of variable frequency drives for fan motors and pumps with advanced control logic.
- Economizers
- Superheathers
- Condensate Management
- Steam Flow Optimization
Success Cases
Legacy of the Rubiales Project
From Metapetroleum to becoming part of Ecopetrol as Campo Rubiales, this project has been an example of growth and transformation in Colombia’s energy sector.
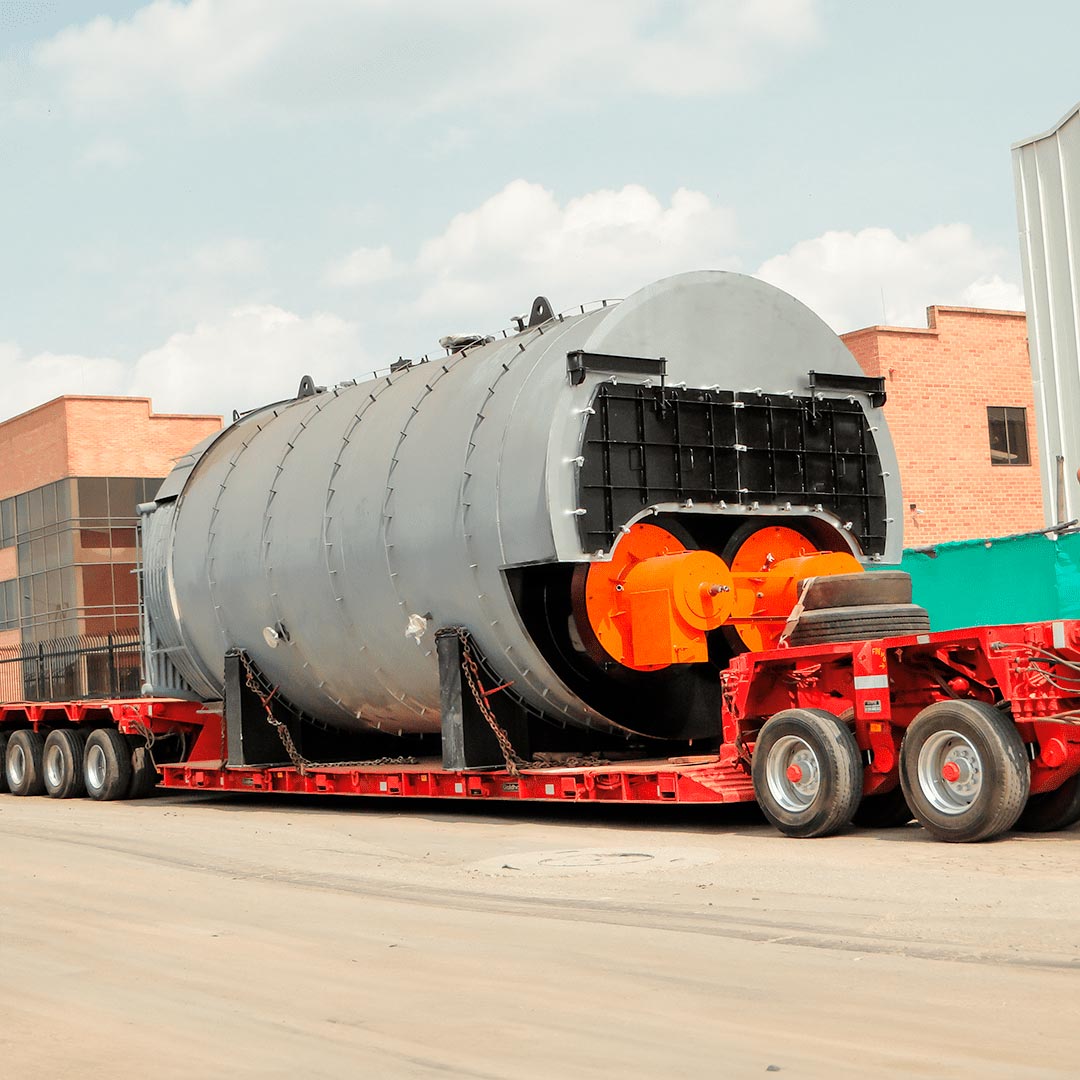
METAPETROLEUM
- 5 BOILERS:
With a capacity of 60,000 lb/hr - FUEL:
Crude – A.C.P.M - FUEL CONSUMPTION:
3,863 lb/h - CAPACITY:
60,000 lb/h with water feed at 105°C - MAXIMUM OPERATING PRESSURE:
170 psi - DESIGN PRESSURE:
250 psi - MAXIMUM STEAM TEMPERATURE:
375 ºF - FUEL SUPPLY PRESSURE TO THE BURNER:
30-35 psi - EFFICIENCY:
86.8%
This project is of the fire-tube type with an aquatubular chamber, equipped with a water preheater. It is designed to operate with heavy crude oil as the primary fuel and ACPM as an alternative. The system includes an induced draft fan, a cyclone for gas treatment, and an economizer, meeting the highest standards of efficiency and safety. Additionally, all necessary accessories are provided, such as a burner and combustion system, an electrical panel, bag filters, and an ash screw conveyor, ensuring complete and reliable operation.
METAPETROLEUM
- 5 BOILERS:
With a capacity of 60,000 lb/hr - FUEL:
Crude – A.C.P.M - FUEL CONSUMPTION:
3,863 lb/h - CAPACITY:
60,000 lb/h with water feed at 105°C - MAXIMUM OPERATING PRESSURE:
170 psi - DESIGN PRESSURE:
250 psi - MAXIMUM STEAM TEMPERATURE:
375 ºF - FUEL SUPPLY PRESSURE TO THE BURNER:
30-35 psi - EFFICIENCY:
86.8%
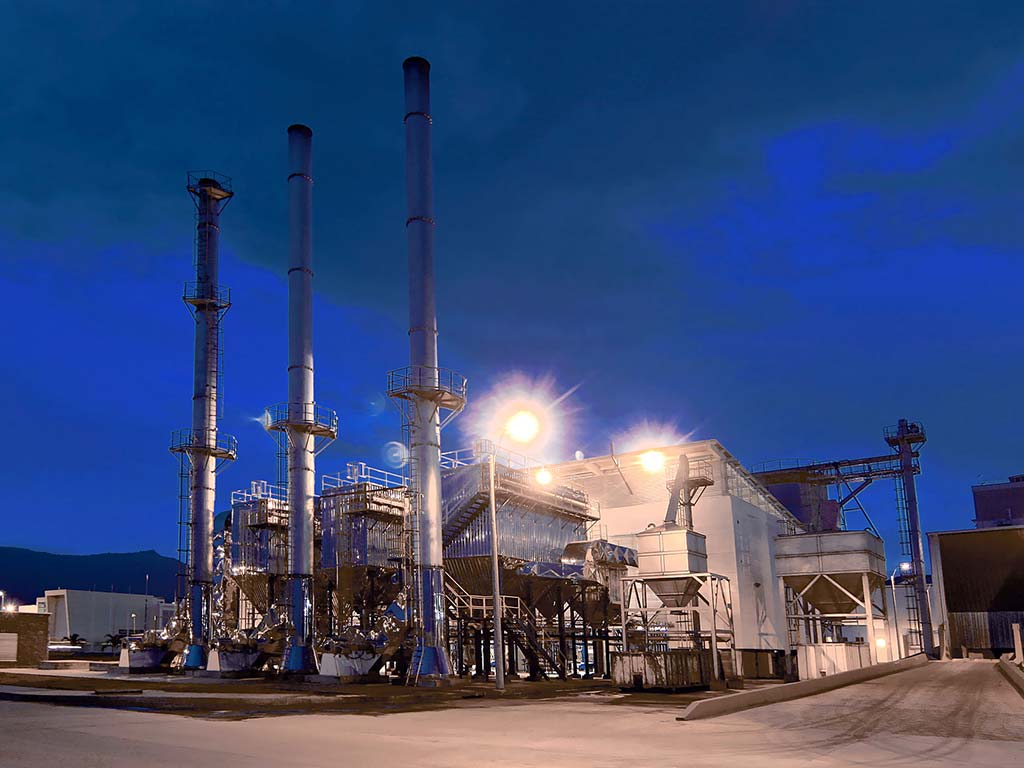
CERVALLE
- FUEL:
Coal and Natural Gas - NUMBER OF BOILERS:
3 Boilers of 1100 BHP - CAPACITY:
17,000 kg/h of saturated dry steam with water feed at 110°C - MAXIMUM OPERATING PRESSURE:
120 psig - DESIGN PRESSURE:
180 psig - EFFICIENCY:
87.4% (with coal)
93.0% (with natural gas)
This project includes three combined boilers equipped with a traveling grate, designed to operate with coal as the primary fuel and natural gas as an alternative. The system guarantees high efficiency and precise combustion control, meeting the highest quality and safety standards according to the ASME code.
CERVALLE
- FUEL:
Coal and Natural Gas - NUMBER OF BOILERS:
3 Boilers of 1100 BHP - CAPACITY:
17,000 kg/h of saturated dry steam with water feed at 110°C - MAXIMUM OPERATING PRESSURE:
120 psig - DESIGN PRESSURE:
180 psig - EFFICIENCY:
87.4% (with coal)
93.0% (with natural gas)
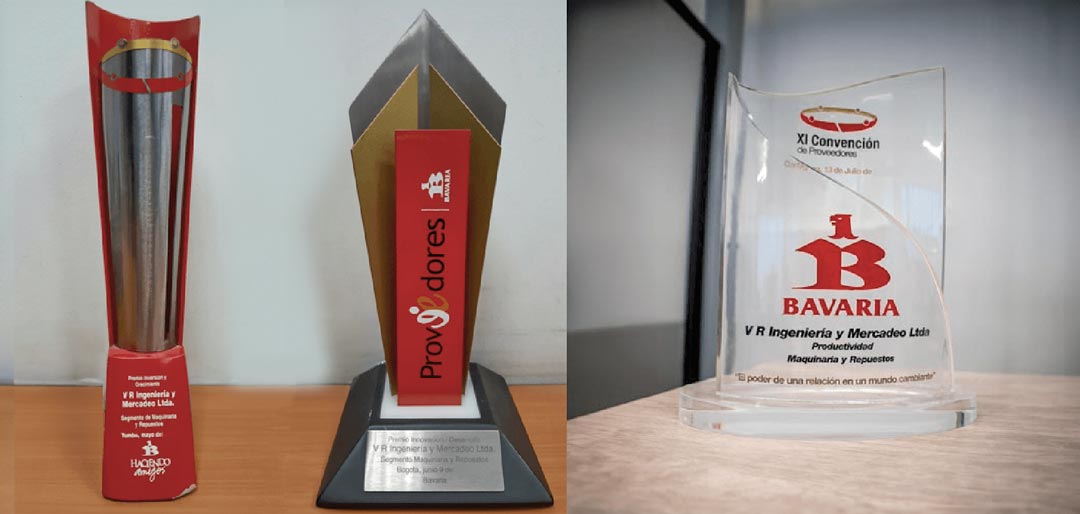
Bavaria Recognition
Cervecería del Valle – Bavaria has honored us with its prestigious awards, recognizing our effort and contribution to the industry.
Bavaria Recognition
Cervecería del Valle – Bavaria has honored us with its prestigious awards, recognizing our effort and contribution to the industry.
Our Valuable Client Portfolio
Here we present a brief list of clients who have trusted our expertise and quality in the development of steam generation systems.
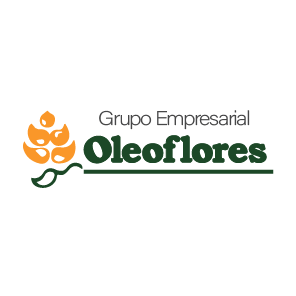
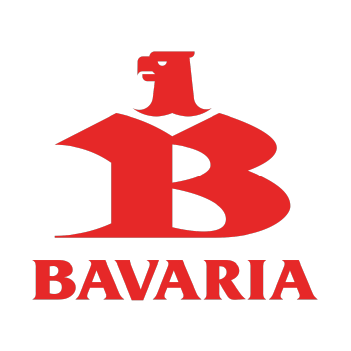
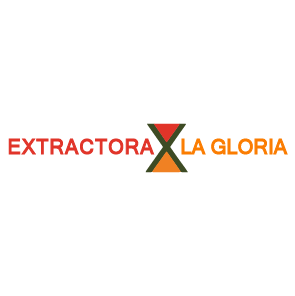
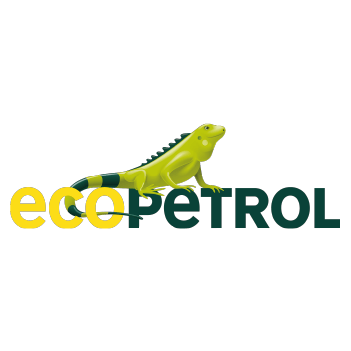
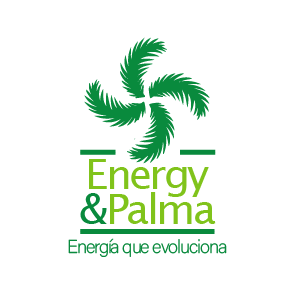
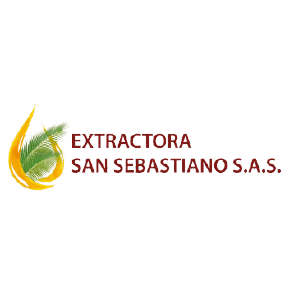
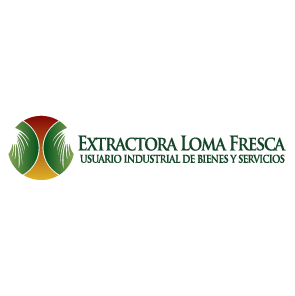
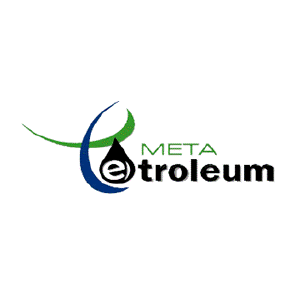
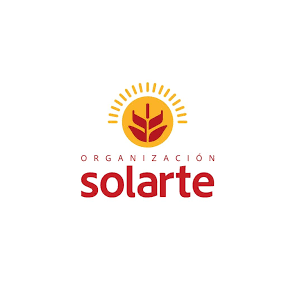
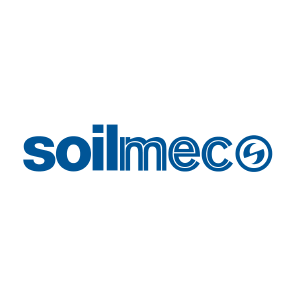
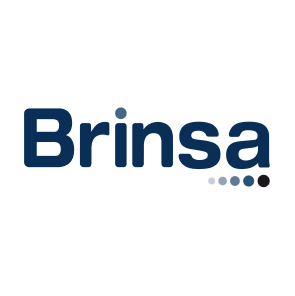
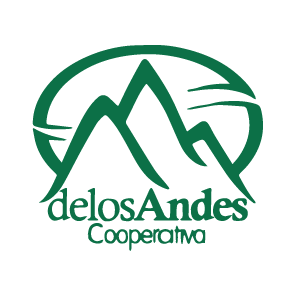
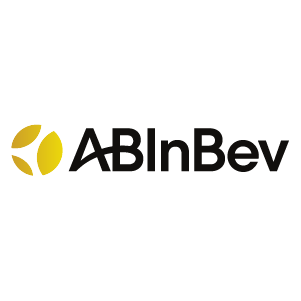
Steam Generation Systems with
High Quality
We specialize in the construction of steam generation systems; all our steam generators are designed and manufactured according to the guidelines of ASME Section I, meeting the highest standards and delivering the most reliable and durable products on the market.
Contact us
Do you have any questions or need more information? Don’t hesitate to write to us. We are ready to help you with whatever you need.